The question drives improvement. Our tendency to ask why is an integral part of the Timber Age™ culture and encourages our teams to address three important challenges...
Problem one:
People aren't "sticking" in rural communities like our hometown of Durango, CO. When people aren't sure if they can stick in a community for the long term, those people are less likely to invest in community. A lack of high quality, affordable housing is a major contributing factor to this issue.
Problem two:
A shrinking skilled labor force, particularly in rural communities, is making the lack of affordable housing worse. Scarcity drives prices up, and when four people leave the trades for every one who joins, 90% of construction projects are over-budget and behind schedule.
Problem Three:
The forests in the Western US are unhealthy. Our forests are overcrowded and more susceptible to disease and death. These tightly-bunched trees and higher levels of drought contribute to record-breaking wildfires every year. In our local forests alone, over one million board feet of wood must be removed from the forest every year for the next twenty years to approach natural stand densities. Much of this wood was previously unused, resulting in wood decomposing or being burned in forest fires or fireplaces.
Forest health is a hot topic, particularly in the west. With drought, and density contributing to mortality rates of trees, it is no wonder we are seeing larger wildfires threaten urban/forest interface communities more often. There is widespread belief that all logging is bad, however, when done responsibly and sustainably forest treatment can truly benefit the forest.
Timber Age™ utilizes Ponderosa Pine harvested with modern low impact equipment to reduce the likelihood of fire. Through utilization in our building system, we provide a carbon-sequestering outlet for the wood. This prevents the typical destinations of burn piles, forest fires or simply rotting on the forest floor. Either process produces carbon that is released into the atmosphere. By using wood in durable building assemblies, we sequester that carbon for 100 years or more.
We are always looking for ways to bring the work forward at Timber Age™, design and planning are no exceptions. One of the issues plaguing the building industry is a tendency for projects to be over schedule and over budget. While this is in no small part due to material sourcing issues, design and planning also play a role. It is much easier for many parties involved to make changes to a structure (out of necessity or want) even after the structure has started to go vertical causing costly delays to the customer.
The inherent need to finalize designs early to accommodate off-site building, combined with Timber Age's desire to improve upon build time and labor efficiency have led us to provide well defined requirements and processes for designing with the Timber Age™ Modular Building System (TAMBS).
Modular has become a bit of a dirty word when talking about affordable housing. Typically it invokes images of rickety structures that end up falling apart after twenty years. Even the 'high end' modular structures developed in recent years typically don't meet the standards of traditional stick built homes. In addition, shipping a box of air is logistically very inefficient.
Don't get us wrong, traditional modular and manufactured homes serve an important purpose in the market, but what if there was a better way? By occupying a middle ground between fully factory built units and traditional building, Timber Age™ can be the best of both worlds. We build a highly durable, panelized system that can be shipped flat, with almost zero wasted space and reduce on-site build times while providing better, safer, more consistent, and fulfilling work for our people.
When talking about building most people think of energy when they hear efficiency. Energy efficiency is an inherent quality of every TAMBS structure. Our standard panel is thermally broken, R-52, and air sealed using two membrane layers. This not only future proofs our system for years of building code updates, it makes the system easily adaptable to Passive House standards.
Off-Site building allows us to pull much of the work of building a house forward in the process. This enables us to have a building dried in after a matter of days instead of weeks, or months. Time to occupancy is reduced with the ability to perform site prep and assembly of structural components at the factory simultaneously. Our panels come up to 10' x 20' sections, enabling entire walls and roof pitches to be set at once drastically reducing time to occupancy.
Forest health is a hot topic, particularly in the west. With drought, and density contributing to mortality rates of trees, it is no wonder we are seeing larger wildfires threaten urban/forest interface communities more often. There is widespread belief that all logging is bad, however, when done responsibly and sustainably forest treatment can truly benefit the forest.
Timber Age™ utilizes Ponderosa Pine harvested with modern low impact equipment to reduce the likelihood of fire. Through utilization in our building system, we provide a carbon-sequestering outlet for the wood. This prevents the typical destinations of burn piles, forest fires or simply rotting on the forest floor. Either process produces carbon that is released into the atmosphere. By using wood in durable building assemblies, we sequester that carbon for 100 years or more.
We are always looking for ways to bring the work forward at Timber Age™, design and planning are no exceptions. One of the issues plaguing the building industry is a tendency for projects to be over schedule and over budget. While this is in no small part due to material sourcing issues, design and planning also play a role. It is much easier for many parties involved to make changes to a structure (out of necessity or want) even after the structure has started to go vertical causing costly delays to the customer.
The inherent need to finalize designs early to accommodate off-site building, combined with Timber Age's desire to improve upon build time and labor efficiency have led us to provide well defined requirements and processes for designing with the Timber Age™ Modular Building System (TAMBS).
Modular has become a bit of a dirty word when talking about affordable housing. Typically it invokes images of rickety structures that end up falling apart after twenty years. Even the 'high end' modular structures developed in recent years typically don't meet the standards of traditional stick built homes. In addition, shipping a box of air is logistically very inefficient.
Don't get us wrong, traditional modular and manufactured homes serve an important purpose in the market, but what if there was a better way? By occupying a middle ground between fully factory built units and traditional building, Timber Age™ can be the best of both worlds. We build a highly durable, panelized system that can be shipped flat, with almost zero wasted space and reduce on-site build times while providing better, safer, more consistent, and fulfilling work for our people.
When talking about building most people think of energy when they hear efficiency. Energy efficiency is an inherent quality of every TAMBS structure. Our standard panel is thermally broken, R-52, and air sealed using two membrane layers. This not only future proofs our system for years of building code updates, it makes the system easily adaptable to Passive House standards.
Off-Site building allows us to pull much of the work of building a house forward in the process. This enables us to have a building dried in after a matter of days instead of weeks, or months. Time to occupancy is reduced with the ability to perform site prep and assembly of structural components at the factory simultaneously. Our panels come up to 10' x 20' sections, enabling entire walls and roof pitches to be set at once drastically reducing time to occupancy.
Off-Site Construction Done Better
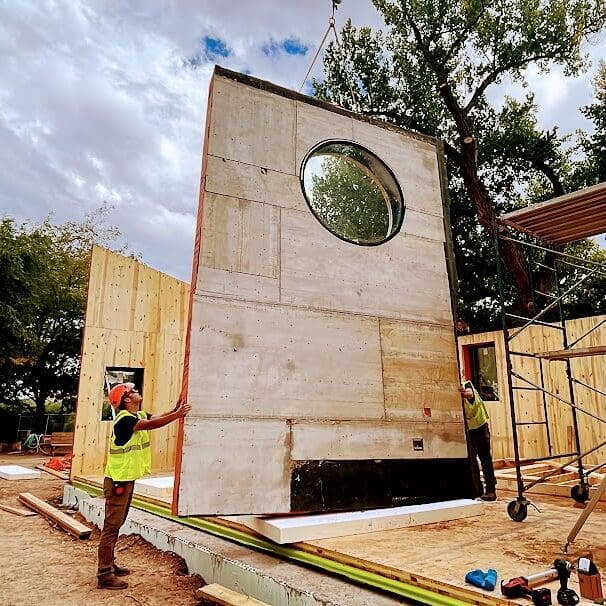
Unfortunately, modular and manufactured construction have become associated with lower quality in recent years. Even the higher end modules tend to use, at most, code minimum construction that is inefficient to transport, inefficient to heat and cool, and not designed to last more than 50 years. TAMBS attempts to bridge the gap between traditional and off-site construction and address some of these shortcomings by providing a durable, efficient, panelized system that can last 100 years or more
Old Technology at a Community Scale

Cross Laminated Timber (CLT) is the backbone of TAMBS. This incredible material allows us to utilize locally harvested Ponderosa Pine, a species not typically used in buildings today. Using local wood harvested for fire mitigation allows us to sequester carbon from trees that would have otherwise been burned or left to rot, releasing that carbon in to the atmosphere. By shortening our supply chain we are also able to reduce transportation costs, lowering the embodied carbon in our structures.
Easy Button for Future Code Compliance
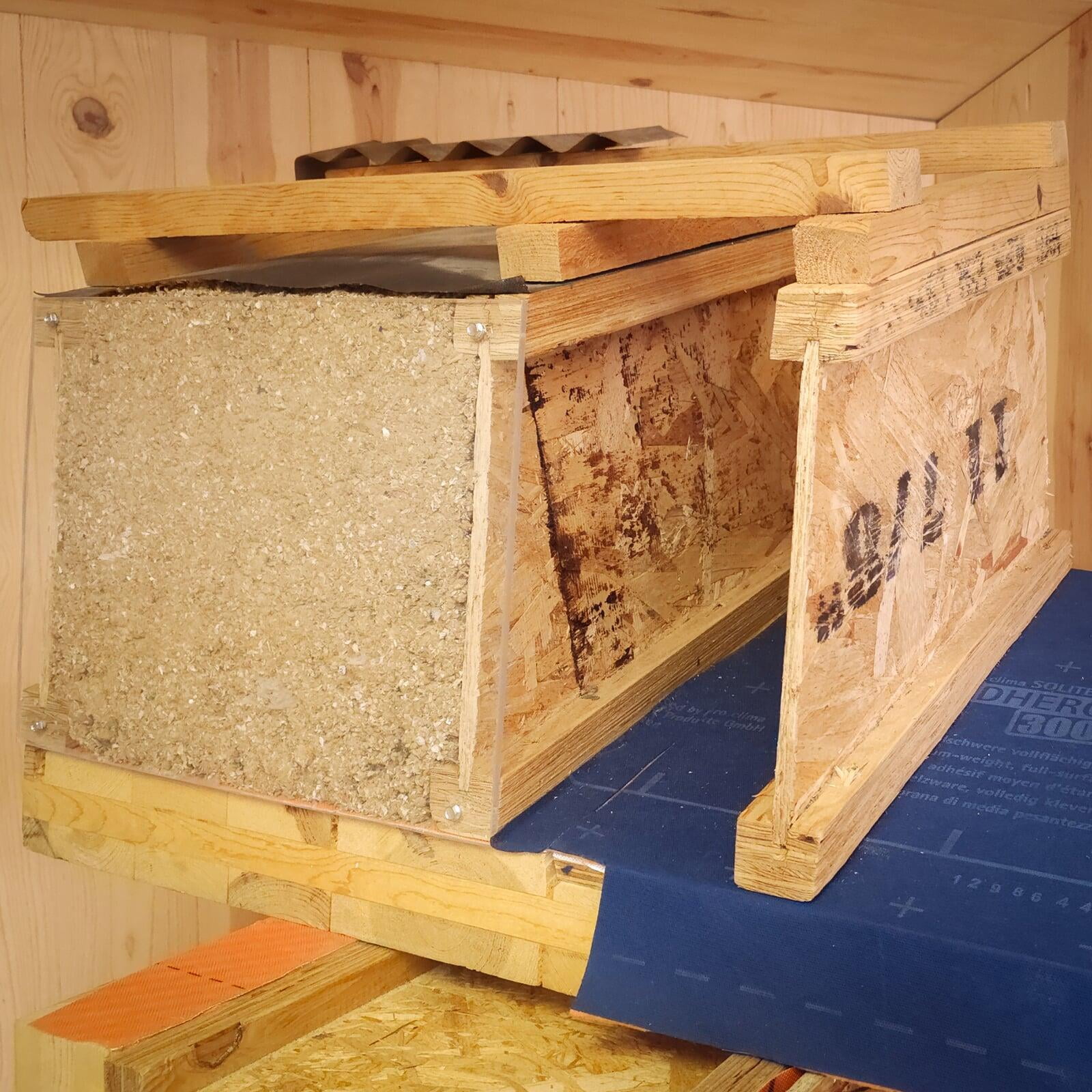
With 12 inches of dense pack cellulose insulation and two layers of continuous membrane, TAMBS is ultra efficient. Achieving and insulation value of R-52, 10x the air tightness of typical construction and a completely thermally broken assembly, TAMBS will surpass code requirements for decades to come.
Scalable Structural Components
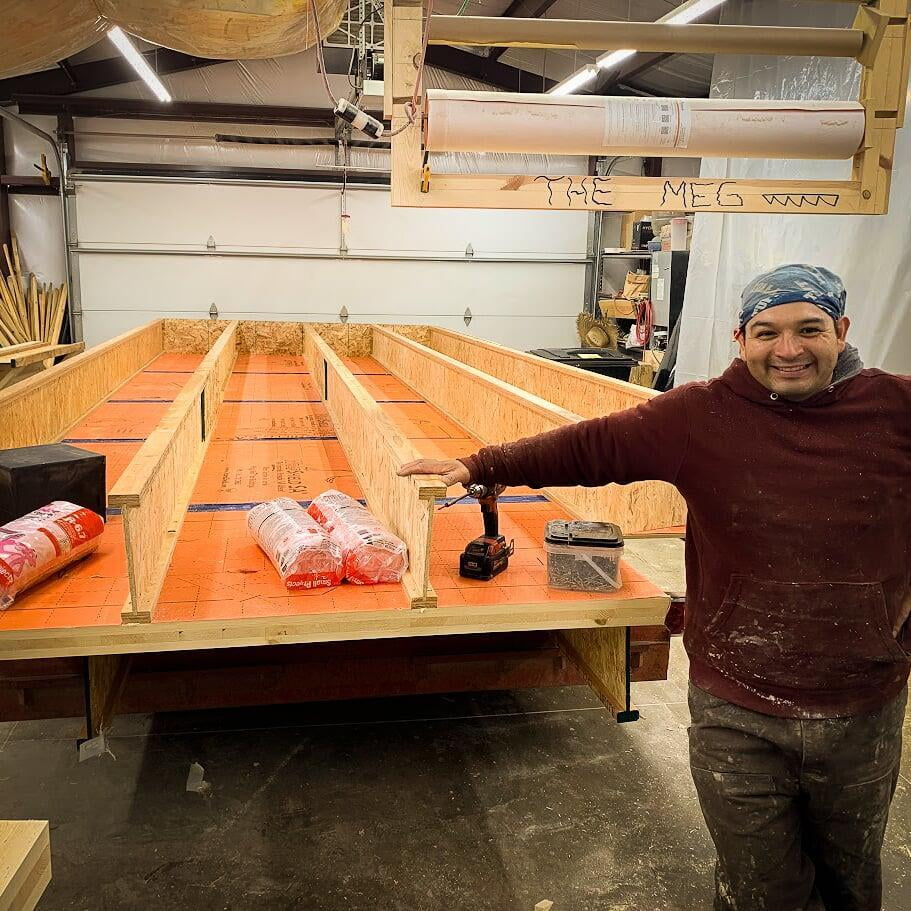
By utilizing a base CLT panel size of 5' x 10' and combining them with structural I-Joists in up to 10' x 20' assemblies, we are able to accommodate almost any dimension for a structural envelope. Starting with smaller components also allows us to utilize smaller facilities more suited to rural communities and residential construction.